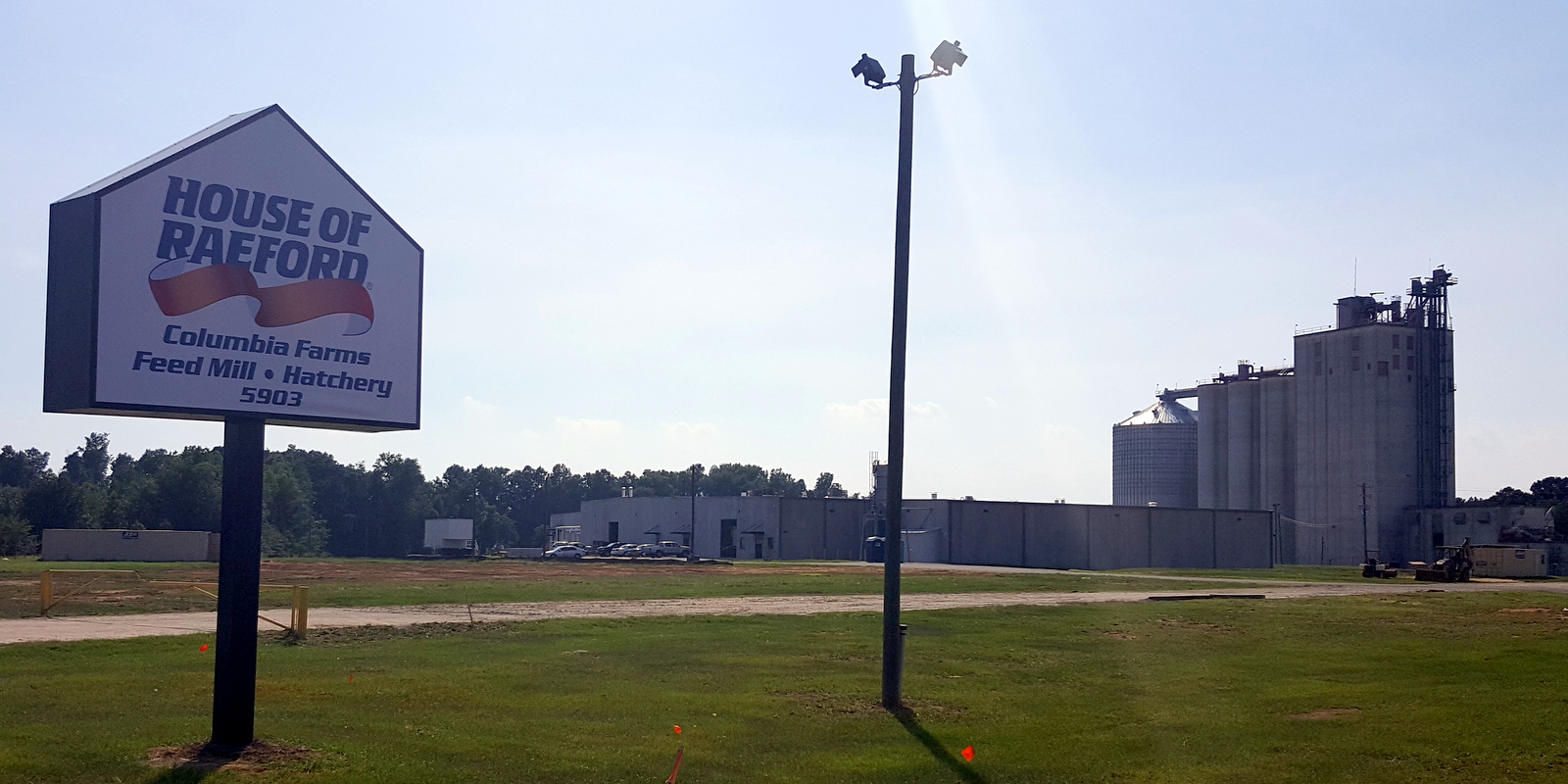
House of Raeford to cut ribbon on multi-million-dollar hatchery
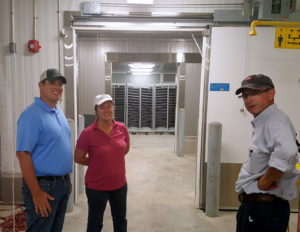
It’s like going from Noah’s Ark to the USS Enterprise.
That’s how David Rush described the technology blitz incorporated into House of Raeford’s new hatchery, just outside of Batesburg-Leesville, on Columbia Highway, in Monetta.
Rush is the Assistant Complex Manager for House of Raeford, Columbia. The new facility is upfitted with the latest advancements from PAS Reform.
The hatchery features advanced technology designed for optimum production efficiency, and it is fully automated to allow for the highest levels of biosecurity, quality control and operational analytics.
Gayle Sharpe, of Batesburg-Leesville, the manager of the hatchery.
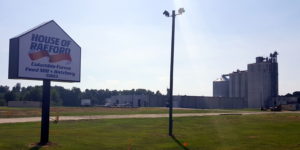
The state-of-the-art, 63,000-sq-ft. facility is being shown off Wednesday- during a ribbon cutting- to company officials and state and local dignitaries. It cost $16 million to build and it will go into full operation on June 22.
“This is an investment for our growers,” said Chuck Underhill, assistant sales manager at Columbia Farms in West Columbia. He also said it it shows House of Raeford’s commitment to the community it serves. “We will be here for a long time.”
During a tour of the building Sharpe said eggs will come in one end and go out the other as healthy baby chicks. Then the chicks will be delivered to county growers, and growers in surrounding counties.
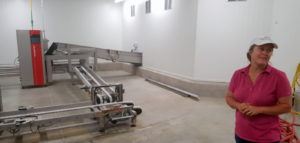
Once mature, the chickens will be processed at House of Raeford’s Columbia Farms plant in West Columbia. The new hatchery will employ 20 people, and is expected to produce more than one million birds per week. It has the capacity to produce up to 3.7 million chicks a cycle.
During the tour of the facility, Rush said there are 30 incubators in the hatchery, each one can hold almost 125,000 eggs. Those eggs are strictly monitored and climate-controlled for 18.5 days. After they hatched, the chicks are moved via conveyor to a room where egg shells are dumped. The birds are also vaccinated twice, said Sharpe. Once while still in the shells.
The eggs and chicks are well-guarded, and so are the humans working on the site.
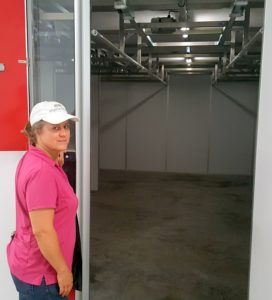
“You have to shower before you enter the building,” Rush said. Every precaution is made to prevent any bacteria or disease from harming the birds.
“We want the healthiest product available to give to our growers,” Underhill said.
The new facility will replace machinery that is more than 60 years old, in some cases, Sharpe said. And all of it can be controlled from off-site locations, if needed.